In 2009, a small workshop in Tumwater was established with the modest intention of storing and marketing high-performance building supplies. They tampered with new ideas to increase home efficiency while selling tapes and membranes to seal homes from the elements.
Now, after fourteen years, Small Planet Supply manufactures a high-capacity, high-efficiency heat pump for apartment and commercial buildings that “talks” to the grid to draw electricity when it’s not needed.
A company that grows from a supplier to a manufacturer is undergoing a transformation. In order for this kind of change to take place, workers also need to adapt and adopt a new way of working. That is precisely what the state’s Job Skills Program assists with.
The Job Skills Program funds training and reskilling initiatives while putting companies in touch with recognized Washington colleges. It facilitates the metamorphosis of companies and their workers. In addition, Small Planet Supply and more than 1,000 other Washington-based companies have expanded during the course of the program’s 40 years.
The Job Skills Program in Washington has been in place for 40 years. The Legislature launched the program in 1983 with the goal of assisting workers and companies in adjusting to changing technologies and competitive pressures. The program assists in training potential personnel to expedite early operations at the opening of a new factory. When an industry changes, the program assists its employees in learning about new areas. Additionally, the program helps employees hone cutting-edge abilities in areas where businesses are pushing the boundaries.
Businesses can easily sell it. On the company’s schedule, employees receive on-the-job training tailored to their particular needs. To create specialized training, employers collaborate with nearby community or technical institutions, public and nonprofit universities, and accredited private career schools. Additionally, they only cover 50% of the training’s cost in kind, such as wages and supplies, or in cash.
According to Carolyn McKinnon, the State Board’s program manager, “employees learn valuable skills that will help them in their careers for years to come, and employers get exactly the training they need on their schedule and location.”
Both communities and workers benefit from it. Employees in specializations where demand is declining can diversify, and aspirational young professionals can be exposed to alternative fields. High unemployment rates can be used to foster entrepreneurship and build a labor force that will draw in new businesses.
The program has trained almost 75,000 professionals in Washington since it began in 1983.
The State Board for Community and Technical Colleges’ executive director, Paul Francis, stated, “The Job Skills Program changes businesses and changes lives.” “The program is a vital tool that helps communities facing high unemployment, supports new and emerging industries, and improves employee skills.”
The CEO of Small Planet Supplies, Albert Rooks, moves quickly. After reading a New York Times article about a “passive house” building, he launched his company. Years later, he was convinced that a shift to manufacturing would be profitable due to Washington State’s support of renewable energy and energy-efficient buildings.
After contacting Impact Washington for guidance on his development, Rooks was advised to apply for a grant through the Job Skills Program in order to assist in upskilling employees. Following the grant’s approval, several floor employees at Small Planet Supply pursued new skills, and managerial staff members started completing factory management courses.
Former warehouse worker Ryan Shepp started a laser-cutting course so he could fabricate unique parts and contribute to production. Shepp’s new title is “manufacturing supervisor,” and because of his accuracy in creating unique parts for their products, he plays a vital role at Small Planet Supply.
Slowly heading to a new direction
Seattle-based Satsuma Designs is a contract cut-and-sew company. In addition to creating an organic baby clothing line, they also handle contract work for well-known national and international brands, including Swaddle Designs, Hardmill, and Freeman. The company is doing well, but things weren’t always like that.
Before switching sides, CEO Jennifer Porter worked for 16 years as a wholesale buyer of sewn items and school uniforms. Porter pledged to take up manufacturing herself after a significant supplier closed and relocated operations overseas. When she was ready to start producing school uniforms in February 2020, she had to search for a location and set up manufacturing for nine months.
Porter was forced to make a change because the epidemic reduced the market for school uniforms. She contacted Impact Washington and was successful in her application for a grant from the Job Skills Program, which allowed her to start retooling her company for contract manufacturing using just-in-time inventory procedures and lean management.
Porter exclaimed, “It’s amazing,” regarding the Job Skills Program. It provided an easy approach to picking up new procedures. I could process the training material and use a fresh approach on my floor the same day.
Porter started incorporating Toyota Kata, Kaizen, Lean, continuous improvement, and other concepts into her company. Using one move after another, her business changed. Every day, as fresh contracts came in, she started asking her employees, “How did it go today? “In order to gauge the relative difficulty of a contract, floor workers would react with a straightforward pleased, neutral, or sad expression. Porter gathered enough information overall to assess contracts, decide how much work to do, and identify the kinds of tasks that should be prioritized.
Porter stated, “In manufacturing, you have to be the highest quality if you want repeat business.” “The JSP provided us with strong tools to hire and develop a talented workforce, obtain contracts, and make plans for the future.”
Satsuma Designs had to start over after a difficult road led to a change in course, but the company is now operating smoothly in part because of the skills acquired from the Job Skills Program.
Porter declared, “I’ve exceeded my hard goals for staff growth and revenue growth.” “I really like that I’m surrounded by women; happiness and laughter are abundant here.”
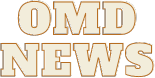